Armor-Plated Fabrics, Superior Savings
Mai 18, 2018
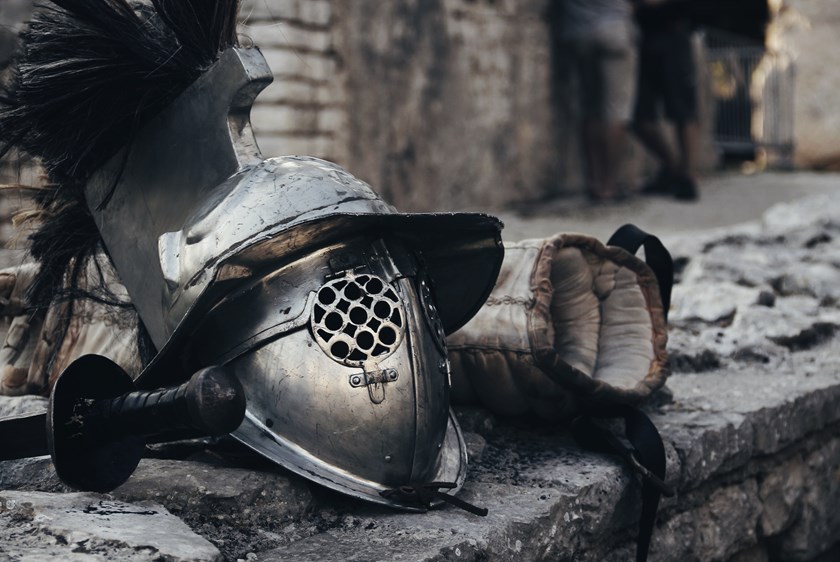
NANOPARTICLES ENABLE LONG-LASTING ENERGY-SAVING SURFACE TREATMENT
Nanotechnology, the manipulation of matter at the “nano scale” of one-billionth of a meter, is helping create products with unique properties. In fact, AstenJohnson used the science to develop a surface treatment for forming fabrics called ArmorTec® that improves cleaning showers and saves energy. Contaminants on a fabric compromise performance, blocking water drainage and creating light spots or pinholes in the paper sheet. Now, papermakers using ArmorTec are seeing a noticeable reduction in the build-up of fibers, stickies, or other contaminants.
Energy savings in excess of 10% have been achieved with ArmorTec.
Microscopic Bumps
The ArmorTec treatment is only several molecules thick, so there is no measurable loss of air permeability in the fabric. In addition, the armor-plated surface creates a large number of very small contact points or “microscopic bumps” where water, oil, and small contaminants can bead up rather than wet the yarns of the interior. The slightest tilt forces beads to roll off under their own weight. And, when vacuum or pressure pulses are applied, the water beads move completely through the fabric, leaving the interior surfaces dry.
ArmorTec maintains its effectiveness over the fabric’s life because even the interior of the yarn surface is treated, and, therefore, not diminished by surface wear.
OLEOPHOBIC EFFECTIVENESS
Oil on fabric without ArmorTec
Oil on fabric with ArmorTec
HYDROPHOBIC EFFECTIVENESS
Water on fabric without ArmorTec
Water on fabric with ArmorTec
The benefits of ArmorTec can really be felt in Through-Air Dried (TAD) tissue production. Here, keeping fabrics clean is essential and traditionally expensive. Cleaning processes account for approximately 16% of the machine’s total energy. However, after conducting TAD conditioning simulations with ArmorTec, researchers reported energy savings in excess of 10%. And when a
North American TAD machine alternated the use of standard and ArmorTec fabric, it achieved average energy savings of 6% with ArmorTec over the approximately 80-day fabric life.